1. Motor Efficiency and Temperature Rise
Inverters, regardless of their type, generate harmonic voltages and currents during operation to varying degrees, causing the motor to run under non-sinusoidal voltage and current conditions. For example, the commonly used sinusoidal PWM inverter has minimal low harmonics, while higher harmonics are typically around 2u+1 (where u is the modulation ratio) and are about twice the carrier frequency. These high-frequency components can significantly affect the performance of the motor.
PWM, or Pulse Width Modulation, is a control technique that uses digital signals from a microprocessor to regulate analog circuits. It is widely used in various applications such as measurement, communication, power control, and conversion due to its simplicity, flexibility, efficiency, and good dynamic response. PWM is often used in switching regulators and is categorized based on the control mode. Other types include PFM, and hybrid PWM-PFM systems. Many modern microcontrollers come with built-in PWM controllers, making it a popular choice for motor control.
Higher harmonics in the power supply can increase copper losses in the stator and rotor windings, as well as iron losses and additional losses. The most significant impact is on the rotor’s copper or aluminum loss, especially in asynchronous motors, which are the most widely used. These motors operate by inducing current in the rotor through the rotating magnetic field of the air gap, hence they are also called induction motors. When higher harmonic voltages pass through the rotor bars at a high slip, large losses occur, leading to increased heat generation, reduced efficiency, and lower output power. Operating an ordinary three-phase asynchronous motor under non-sinusoidal inverter output can result in a temperature rise of 10% to 20%.
2. Motor Insulation Strength
Many small and medium-sized inverters use PWM control, which operates at frequencies ranging from several thousand to tens of kilohertz. This causes the motor's stator winding to experience a very high rate of voltage change, effectively applying a steep voltage to the motor. This places the inter-turn insulation under harsh testing conditions. Additionally, the rectangular pulse voltage generated by the PWM inverter can be superimposed on the motor’s operating voltage, posing a threat to the ground insulation. Repeated exposure to high voltage can accelerate the aging of the insulation system.
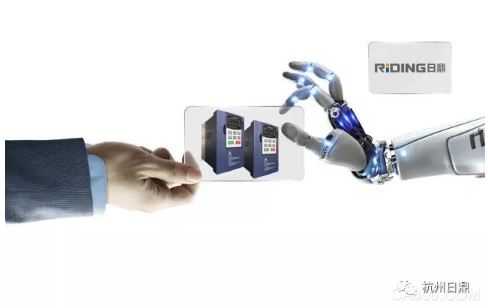
3. Harmonic Electromagnetic Noise and Vibration
When an ordinary asynchronous motor is powered by a frequency converter, the vibration and noise caused by electromagnetic, mechanical, and ventilation factors become more complex. A variable frequency power supply converts AC from the mains into DC and then back to AC, providing a pure sine wave output with adjustable frequency and voltage. Unlike traditional speed controllers or voltage regulators, it closely resembles an ideal AC power supply—stable frequency, stable voltage, and no distortion. Advanced countries increasingly use variable frequency power supplies as standard power sources to provide optimal power environments for electrical devices and facilitate objective performance evaluations. There are two main types of variable frequency power supplies: linear amplification and SPWM switching. The harmonics produced can interact with the motor’s inherent spatial harmonics, creating electromagnetic excitation forces. If the frequency of these forces matches the motor’s natural vibration frequency, resonance occurs, increasing noise levels. Due to the wide operating range of the motor, it is challenging to avoid resonance in different components.
4. Motor Ability to Start and Brake Frequently
Using an inverter allows the motor to start at low frequency and voltage without inrush current, and it can be quickly braked using various braking modes provided by the inverter. This enables frequent start and stop operations, subjecting both the mechanical and electromagnetic systems to cyclic alternating forces. Over time, this leads to fatigue and accelerated aging of the motor’s structure and insulation system.
5. Cooling Problem at Low Speed
First, the impedance of an asynchronous motor is not ideal. At lower frequencies, the losses caused by higher harmonics increase significantly. Second, when a general asynchronous motor runs at a low speed, the amount of cooling air decreases proportionally to the cube of the rotational speed, resulting in poor cooling at low speeds and a sharp increase in temperature. This makes it difficult to maintain constant torque output.
A public account with personality
R&M BOX PRO 6000 Puff is a Disposable Vape Ecig with colorful RGB light and it is rechargable. It contains 10mL of e-liquid and vape up to 6000 puffs. There are 10 flavors for you to choose. RGB lights make it the coolest Disposable Electronic Cigarettes, and a rechargeable USB port on the bottom of the device ensures you use up every drop of e-juice in the can and keep it lit all the time.
1. Newest technology mesh coil with 1.0Ω, smoother and bigger vapor, create the purest taste.
2. Integrated 850mAh A grade Rechargeable battery, don't need to worry battery run out soon .
3. Refillable and equipped 10ml imported E-liquid, fill it at any time and keep e liquid fresh. And you can fill more e liquid if 10ml use out.
4. Implanted 6 colors RGB light on the oil tank, sparkling atmosphere, let the vape no be alone.
5. Unique MOD molding with visual oil tank, classic box mod shape, Cheap price but enjoy a luxury feeling.
Better than better. R&M BOX PRO, your new generation vape device.
If you like Huge vapor, can find the product similar like Fluum Bar 6000 puff,R&M Monster 7000 hit,R&M LEGEND 10000 Puff.R&M 1000 Puffs also good taste.
Disposable E-Cigarette,Vape Box,Vape Mod,R&M BOX PRO
Shenzhen Essenvape Technology Co., Ltd. , https://www.essenvape.com